プラントでも大活躍!配管溶接とは?
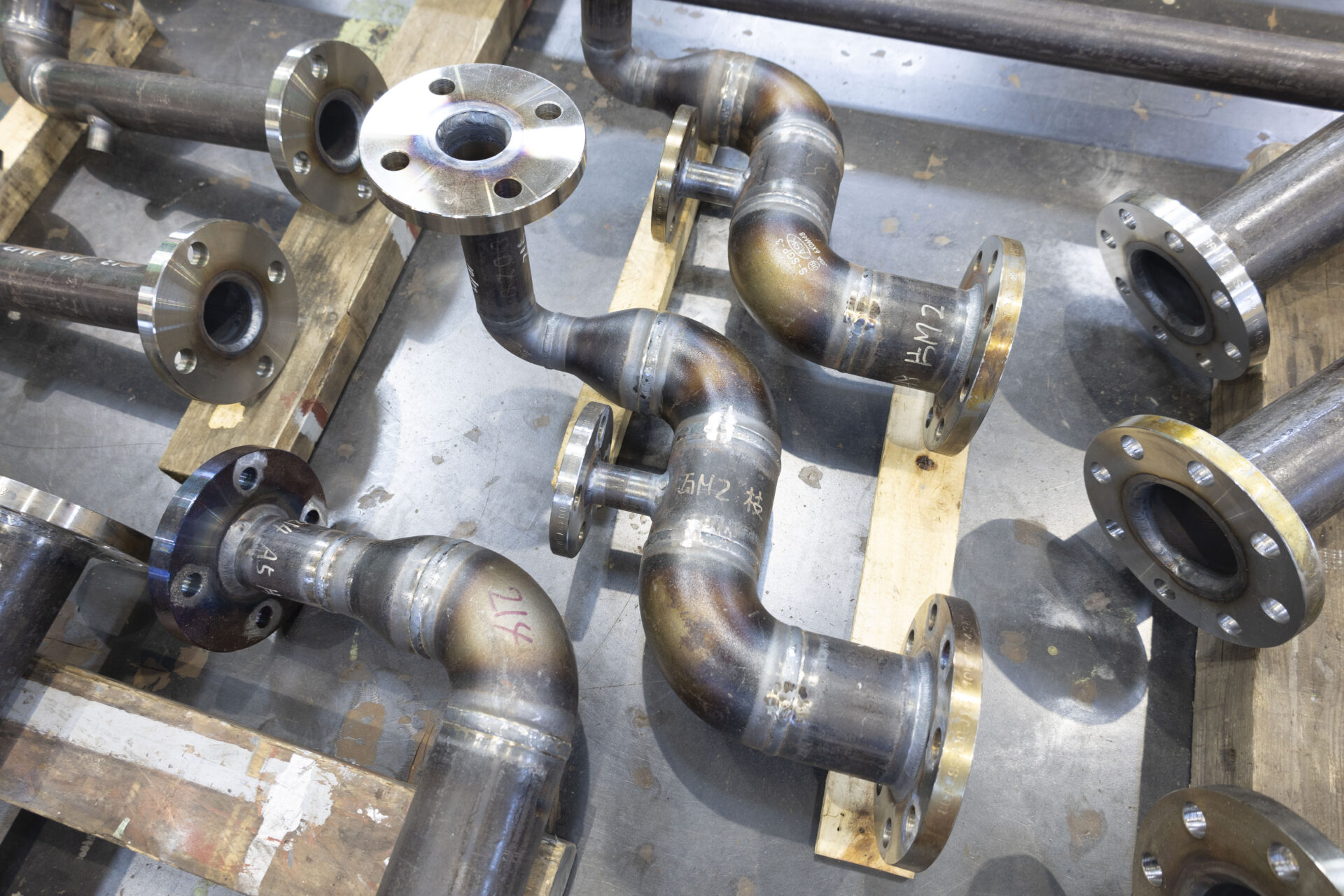
「配管溶接」とは、2本の配管を溶接して繋ぐ方法のことです。配管を繋ぐ方法は溶接の他に、ねじ山を利用して管を回転させて接続する「ねじ込み接続」やパイプ同士をフランジでボルト締結する「フランジ接続」があります。これらの3つの接続方法の中で、最も耐久性が高い接続方法は「溶接」です。ここでは、その配管溶接はどんな仕組みになっているのか紹介します。
配管溶接とは?
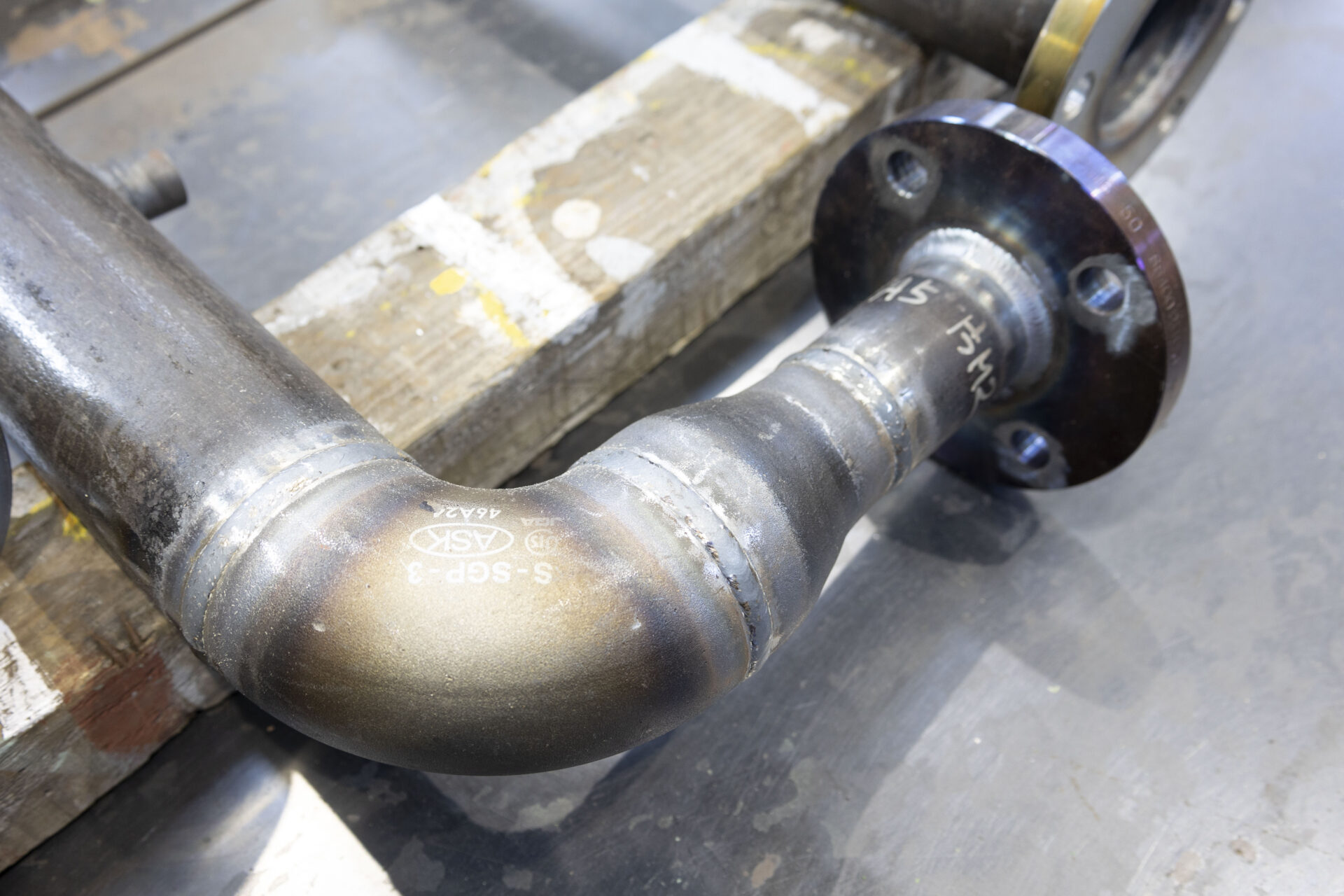
プラントや工場で配管を設置する際に、配管同士を溶接することを「配管溶接」と言います。配管溶接は、高圧や高温の環境下で使用される配管システムの信頼性と耐久性を確保するために非常に重要です。配管の接続方法には、「ねじ込み接続」や「フランジ接続」もありますが、これらは圧力に対して弱い部分があります。そのため、強度が必要な配管部分では、配管溶接が多く採用されます。
ねじ込み接続
ねじ込み接続は、比較的低圧で小口径の機器に多く採用されている接続方法です。接合部に切ったねじ山を用い、「おねじ」と「めねじ」の組み合わせで構成されます。管を回転させてねじ込むことで接続・固定を行います。蒸気系統では、機器側がめねじ、管側がおねじとなることが一般的です。
ねじの規格にはいくつかの種類がありますが、日本国内では「管用テーパーねじ」がほとんど適用されています。テーパーねじは、先端部分の外径よりも終わり部分の外径が大きくなる形状をしています。これにより、ねじ込んでいくとある程度のところで止まり、ねじ山同士の気密性が高まります。この時、シールテープや液状のシール材を併用することで、さらなる気密性を確保します。
長所 | ・工事が容易: 切断機とねじ切り盤があれば、現場合わせの工事が容易に行えます。 ・工数が少ない: 事前準備や工事実施の工数が少なくて済みます。 ・規格が統一: 国内ではねじの規格がほぼ単一であるため、規格に対する統一性があります。 ・機器が小型軽量で安価: バルブやスチームトラップなどの機器が小型で軽量、安価に入手可能です。 ・コスト削減: フランジに比べて、ボルトやガスケットが不要で配管材料費が抑えられます。 |
短所 | ・腐食しやすい: 「おねじ」部先端の肉厚が薄いため、腐食や減肉が起こりやすく、漏れやすいです。 ・高圧には不向き: 高圧では使用できません。 ・脱着が手間: 機器脱着のため、要所にユニオンやフランジを入れる必要があります。 ・大口径には不向き: 大口径ではねじ込み作業が難しいです。 |
一般的な用途 | ねじ込み接続は、小型軽量の機器に多く採用される接続方法です。比較的低圧での使用に適しており、工数が少なくて済むため、現場での即応性が求められる場面においても利用されています。 |
フランジ接続
フランジ接続は、小口径から大口径、低圧から高圧まで広く使用されている接続方法です。配管や機器の接続端に「フランジ」と呼ばれる平板を取り付けることが特徴です。バルブなどの機器には、本体と一体成型されたフランジ部を持つものもあります。
フランジ接続では、管に対して「つば」のように出っ張る部分ができ、この出っ張り部分を利用してボルトナットで固定します。相手方フランジとの間にガスケットを挟み、ボルトナットで締め付けて密着させることで気密性を確保します。
また、フランジの厚みやボルトの穴数、ボルトの太さなどは規格で定められています。日本国内ではJISフランジやJPIフランジがよく使用されますが、それぞれの規格内でも、呼び圧力で細分化されています。呼び圧力とは、バルブ類の圧力区分を示すための表示です。
長所 | ・漏れにくい: 広い面でシールするため、接続部の漏れが少ないです。 ・メンテナンスが容易: 漏れた場合でも増締めやガスケット交換が簡単で、復旧がしやすいです。 ・機器の脱着が簡単: 機器の脱着が容易で、メンテナンスや交換が簡単に行えます。 ・高圧対応: かなりの高圧まで使用可能です。 ・多様なガスケット: 使用可能なガスケットの種類が豊富で、様々な用途に対応できます。 ・増締めが容易: 増締めが簡単に行えるため、定期的なメンテナンスが容易です。 |
短所 | ・溶接作業が必要: 管にフランジを取り付けるには一般的に溶接作業が必要です。 ・工数がかかる: 施工の工数がかかり、現場あわせの工事は難しいです。 ・材料費が高い: 接続部ごとにボルトナットとガスケットが必要で、配管材料費がかさみます。 ・機器単価が高い: 本体にフランジが付く分、バルブなどの機器単価が割高になります。 ・規格の違い: さまざまな規格のフランジが存在し、同サイズでも規格が異なるフランジは接合できません。 |
一般的な用途 | フランジ接続は、その信頼性とメンテナンスの容易さから、あらゆる用途に広く使用されている接続方法です。特に高圧・高温の配管システムや、頻繁にメンテナンスが必要な配管システムなどで重宝されています。 |
溶接
溶接接続は、比較的高圧の接続に使用される方法です。溶接により管同士や管と配管部材や機器が一体化するため、最も信頼性が高い接続方法とされています。しかし、その反面、溶接作業やそれに伴う周辺作業が必要となるため、工事の難易度が高くなります。溶接部は、ソケットやフランジなど、管外径よりも大きい内径を持つ継ぎ手や機器に管を挿入してから溶接する「差し込み溶接」と、管同士(または管と機器)の接続端面を突き合わせて溶接する「突き合わせ溶接」の ふたつの方式があります。
長所 | ・漏れない: 溶接部は漏れのリスクがほとんどない。 ・極めて信頼性が高い: 一体化することで非常に高い信頼性を持つ。 ・高圧対応: 管が使用可能な圧力であれば、どんな高圧でも使用可能。 ・接続部が小さくシンプル: 接続部がシンプルでコンパクト。 ・低コスト: 機器類にフランジが無いため、低コストで済む。 |
短所 | ・施工が難しい: 溶接作業やそれに伴う前処理が難しい。 ・工数がかかる: 前処理や準備に多くの工数が必要。 ・溶接検査が必要: 必要に応じて溶接検査が求められる場合がある。 ・材料制限: 溶接可能な材質にしか適用できない。 ・異種金属の接合が難しい: 異なる金属同士の接合が技術的に難しい。 ・後処理が必要: 溶接後に熱処理が必要な場合がある。 ・取り換えが困難: 機器の取り換えやメンテナンスが難しい場合がある。 |
一般的な用途 | 溶接接続は、高圧高温配管を中心に、信頼性と耐久性を最優先するプラントで多く使用される接続方法です。石油化学プラント、発電所、製鉄所など、高い圧力と温度に耐える必要がある配管システムで広く利用されています。 |
配管溶接は、金属同士を高温で溶融し、冷却・凝固させることで強固に接合します。これにより、金属同士が一体化し、非常に高い耐久性と気密性を実現します。溶接にはさまざまな方法があり、それぞれの方法には特定の用途や利点があります。次の項目では主な溶接方法について特徴を詳しく見ていきましょう。
配管溶接の主な種類

溶接の主な種類は一般的に3種類とされていますが、配管溶接にはさらに多くの方法が存在します。配管システムの設計や使用環境によって、適切な溶接方法を選択することが求められます。ここでは、配管溶接の代表的な溶接方法を紹介します。
被覆アーク溶接
被覆アーク溶接(SMAW)は、母材と同じ材質の金属棒を心線(電極)として使用し、心線と母材との間にアークを発生させ、その熱源で溶接する方法です。この手法は風に強いため、屋外での作業に適しています。また、装置が単純で持ち運びしやすいため、現場での修理などによく用いられます。しかし、使用する溶接棒は太く、大電流のアーク放電が必要なため、薄板の溶接には不向きです。また、他の溶接方法と比べて技術が必要であり、職人の技術力の差で品質が左右される場合があります。
ティグ溶接(TIG溶接)
ティグ溶接(TIG溶接)はアーク溶接の一種であり、融点の非常に高いタングステン電極棒を使用して、溶接したい部分を溶かす方法です。この溶接法では、シールドガスを用いて溶接部を保護することが一般的で、必要に応じて溶加材を接合部に足すことも可能です。ティグ溶接の特徴の一つとして、溶接作業中に火花が散らないことが挙げられ、これにより製品をきれいな状態に保つことができます。ティグ溶接は、高品質で精密な溶接が求められる場合に適しており、ロケットエンジンなどの精密機器の製造に頻繁に使用される手法です。ただし、作業の難易度が非常に高く、熟練の技術力が必要となるため、専門的な訓練と経験が求められます。
マグ溶接(MAG溶接)
マグ溶接(MAG溶接)は、シールドガスに不活性ガスと炭酸ガスを混合して使用するアーク溶接の一種です。また、シールドガスに炭酸ガスのみを使用する場合はCO2溶接と呼ばれます。この方法では、電極として消耗する溶接ワイヤーを使用し、ローラーによって自動供給されます。溶接棒は自動で供給されますが、溶接トーチは作業者が手動で動かすため、半自動溶接とも呼ばれます。
配管で使用される配管材(パイプ)の種類
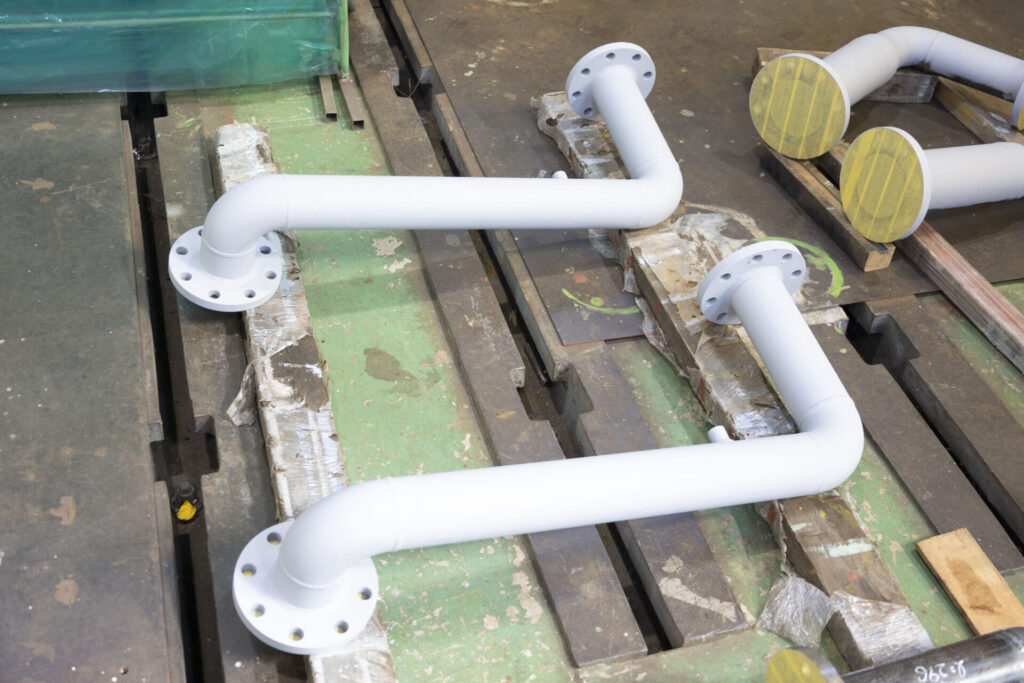
配管で使用される配管材(パイプ)は、大きくシームレスパイプと溶接鋼管の2種類に分けられます。溶接鋼管はさらに3種類に分けられます。以下、それぞれの特徴と適している用途について紹介します。
シームレスパイプ
シームレス管は、継ぎ目のない一体成型のパイプです。 継ぎ目がないため、強度が均一で高い圧力や高温に耐えやすいのが特徴で、高圧配管や高温配管、化学プラントや石油精製設備など、厳しい条件が求められる場所に使用されます。
溶接銅管
溶接鋼管は、パイプの形状に加工された鋼板を溶接して作られるパイプで、以下の3種類に分けられます。
- アーク溶接管
パイプの長手方向の継ぎ手をアーク溶接で接合して製造します。形状によってストレートシーム鋼管とスパイラルシーム鋼管に分けられます。高い強度を持っているのが特徴で、大口径の配管に適しています。長距離のガスや油の輸送、建築や構造物の柱などに使用されます。
- 電縫管
板状の鋼帯を円筒状にした端の部分を溶接して成型します。管の厚みが薄いパイプに適しており、生産性が高く、比較的低コストで製造可能なのが特徴です。水道管、ガス管、暖房設備などの一般配管に使用されます。
- 鍛接管
板状の鋼帯を巻いた状態で加熱した後、成形ロールを通過させて円形上に変形させる製造方法です。高い耐久性を持ち、圧力に強いのが特徴です。 高圧ガスの輸送、石油・ガス産業で使用されます。
弊社の配管溶接加工事例
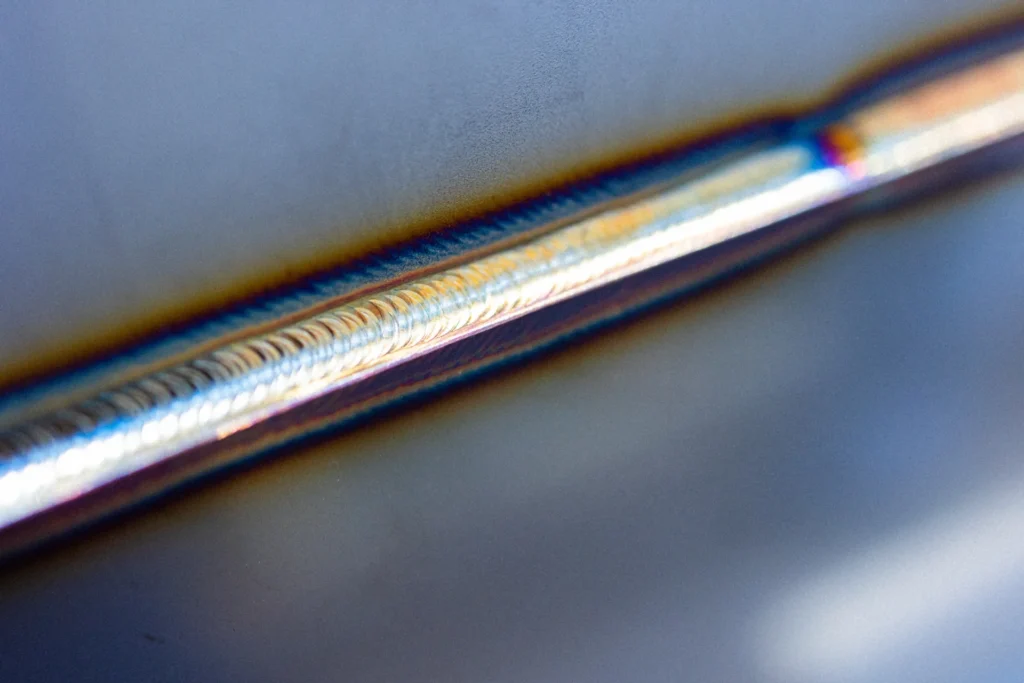
当社で行った溶接のビード
- 発電プラント内 大径管(SUS200A SCH120)溶接
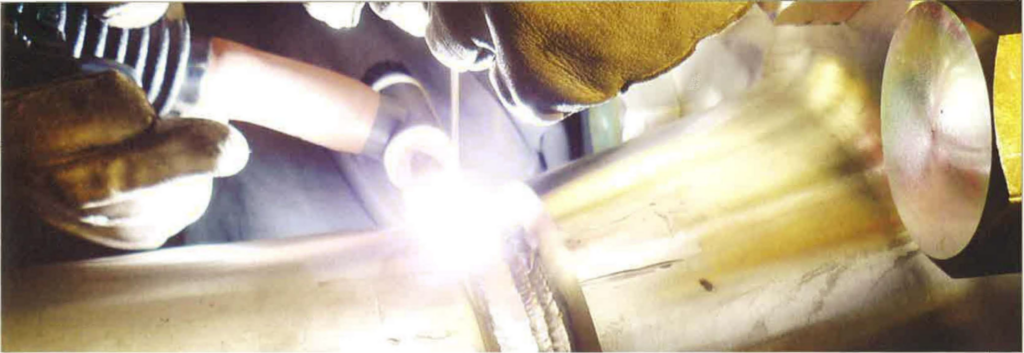
発電プラント内で利用する材質:SUS200A、厚さ:SCH120の大径管の溶接作業です。
高い技術を求められるステンレスかつ厚みを持つ材質なため、歪みを抑えるための予熱や後熱の考慮や
溶接材の選定など、弊社の強みである豊富なノウハウを活かした製品です。
材質 | SUS200A |
厚さ | SCH120 |
開発期間・納期目安 | - |
交差レベル | - |
製品用途 | 発電プラント |
- 計装ラック内配管および耐圧作業
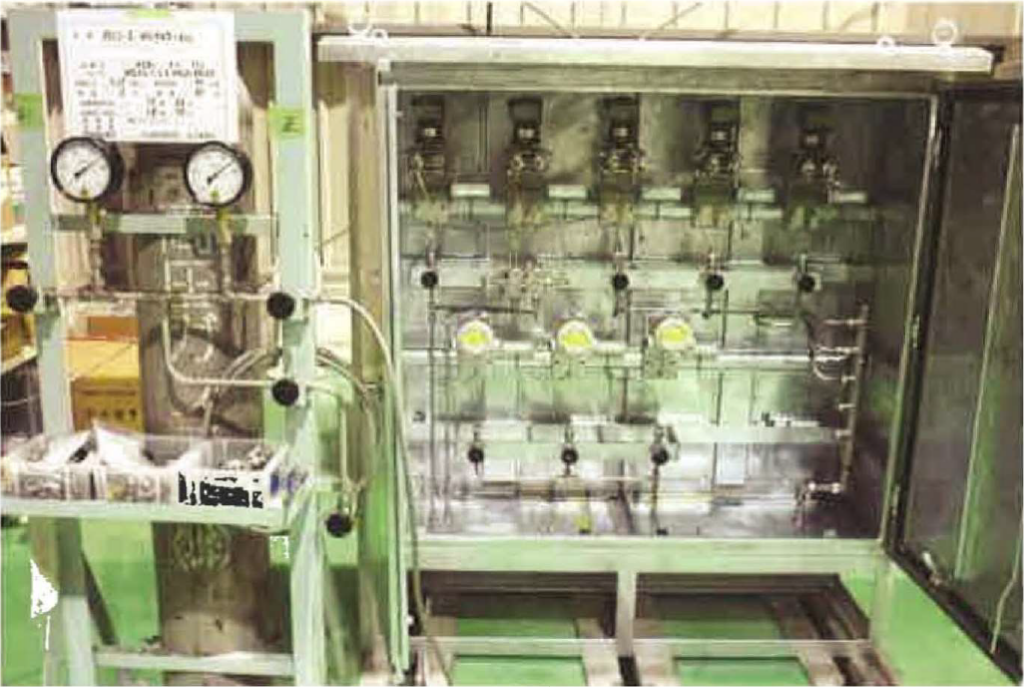
計装ラック内での精密な配管と溶接が求められ、高信頼性が必要とされました。そのため、弊社が主体となり、耐圧試験まで実施しました。日頃から高信頼性を求められるプラント配管を手がけていることで蓄積されたノウハウを活かし、この製品を提供しています。
材質 | - |
厚さ | - |
開発期間・納期目安 | - |
交差レベル | - |
製品用途 | プラント内における流量計測での利用 |
まとめ
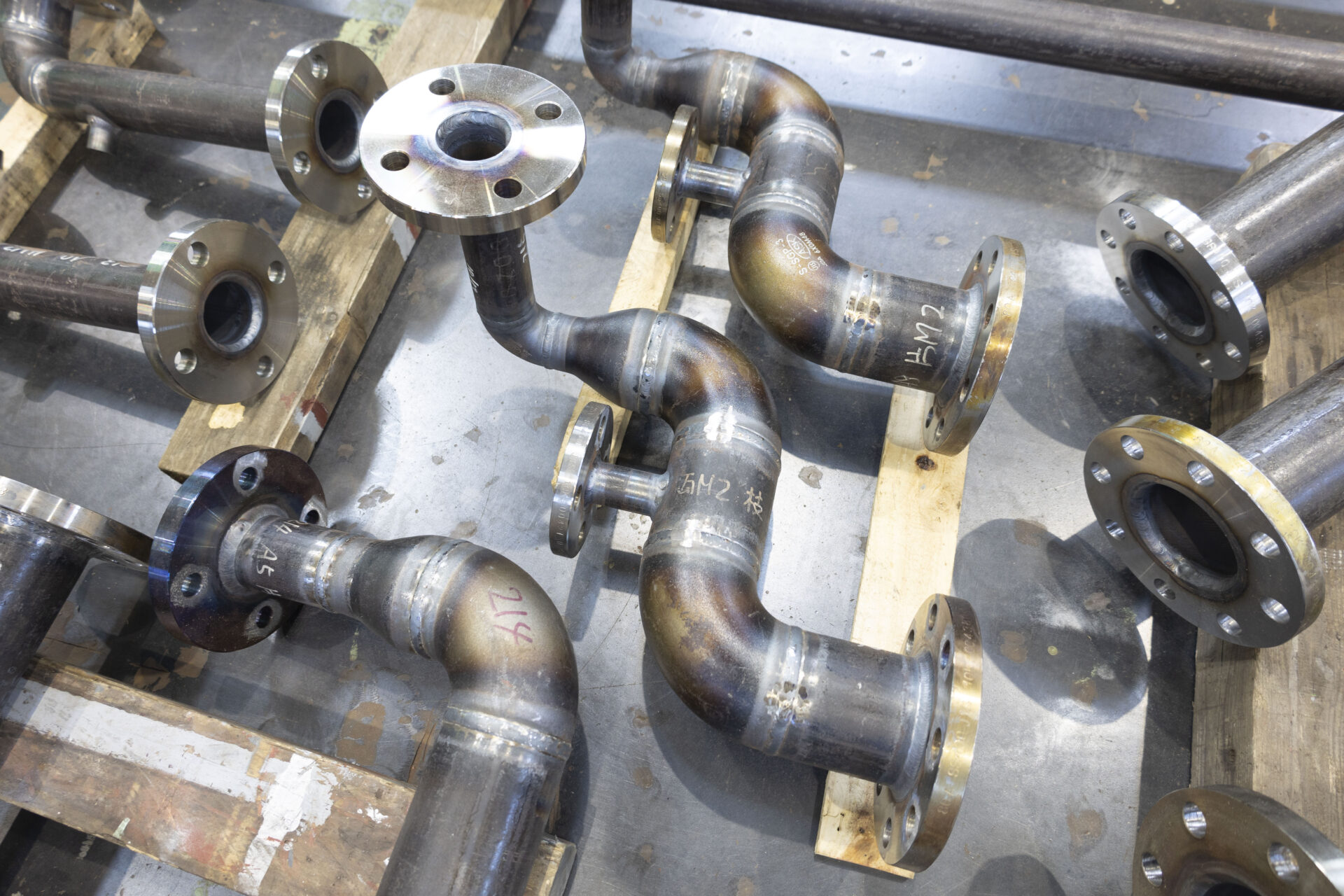
配管溶接はプラントや工場における配管システムの信頼性と耐久性を確保するために重要な役割を果たしています。
配管溶接には様々な方法があり、それぞれの方法が特定の使用用途や要求に応じて最適化されています。適切な溶接方法の選択と正確な技術の実施は、製品の安全性と耐久性を大きく左右します。また、溶接不良を防ぐための対策を理解し、適用することも高品質な製品を保証する上で極めて重要です。
当社では、これまでに培ったノウハウと高品質な溶接技術を基に、現地での据付作業や付帯する鋼構造物製作など、プラント配管に関わる幅広いニーズにお応えしています。その結果、お客様から高い信頼と評価を得ております。
配管溶接のご依頼をご検討中の方は、お気軽に当社までご相談・お問い合わせください。高信頼性を追求した溶接技術と確かな実績で、お客様の多様なニーズにお応えします。
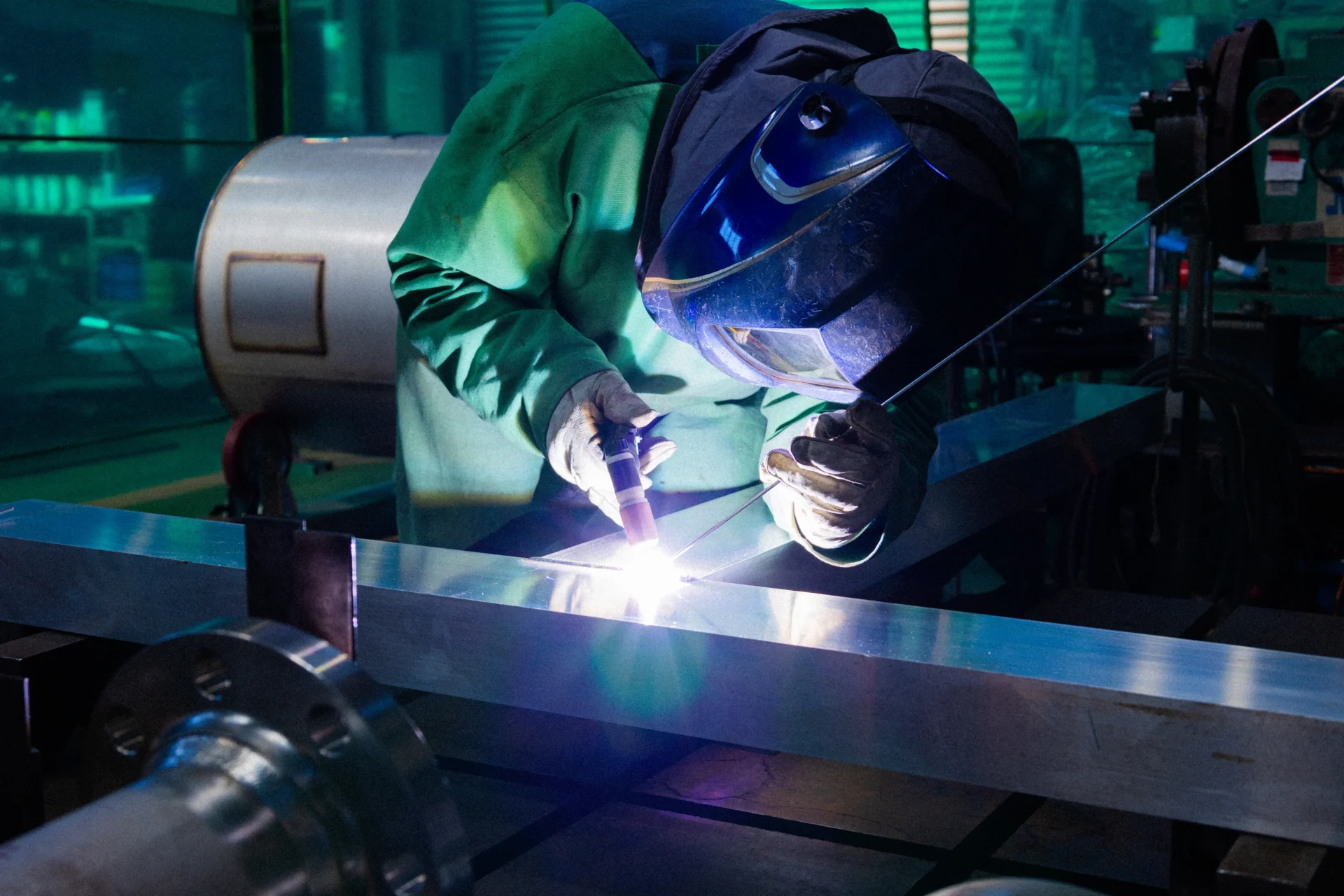
お問い合わせ
ご相談・お見積り依頼などお気軽にお問い合わせください