溶接とは?様々な種類や特徴、基礎知識を解説!
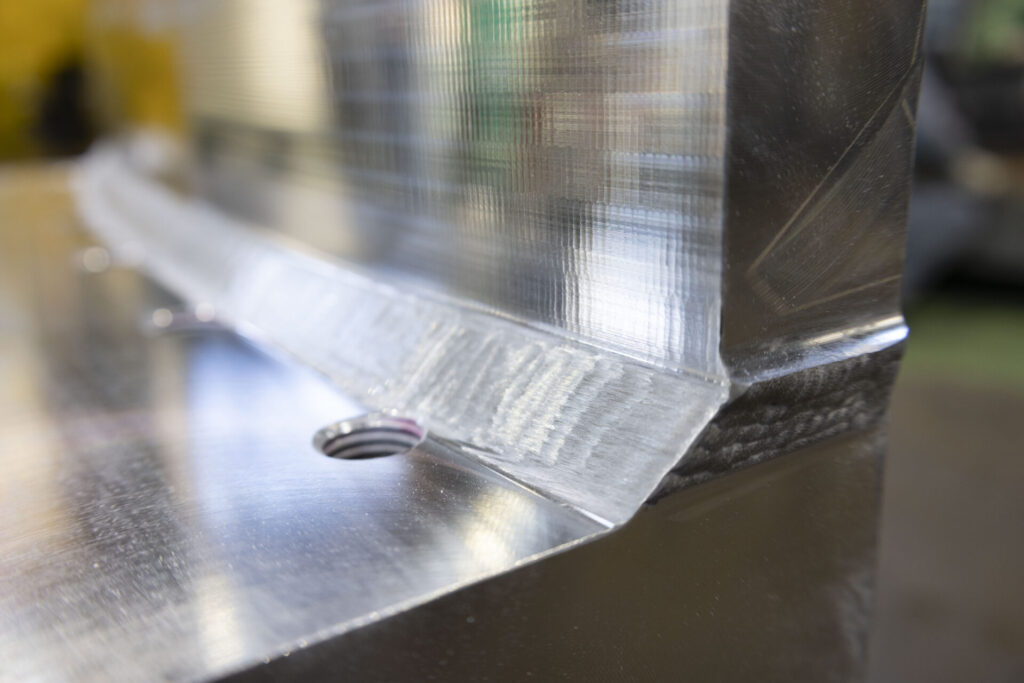
溶接とは、2個以上の部材の接合部に熱や圧力などを加え、接合部を融合・一体化された1つの部材となるよう接合する方法を指します。
溶接は工業的にも非常に重要な役割を果たしており、建設業から自動車製造、造船、航空宇宙産業に至るまで幅広い分野で利用されています。
溶接は金属加工でよく用いられる方法ですが、様々な加工方法の種類があり、各々使用する溶接機が異なっています。
ここでは、溶接の基本的な種類や方法、溶接加工における不良とその対策方法を紹介します。
溶接とは?~基礎知識~
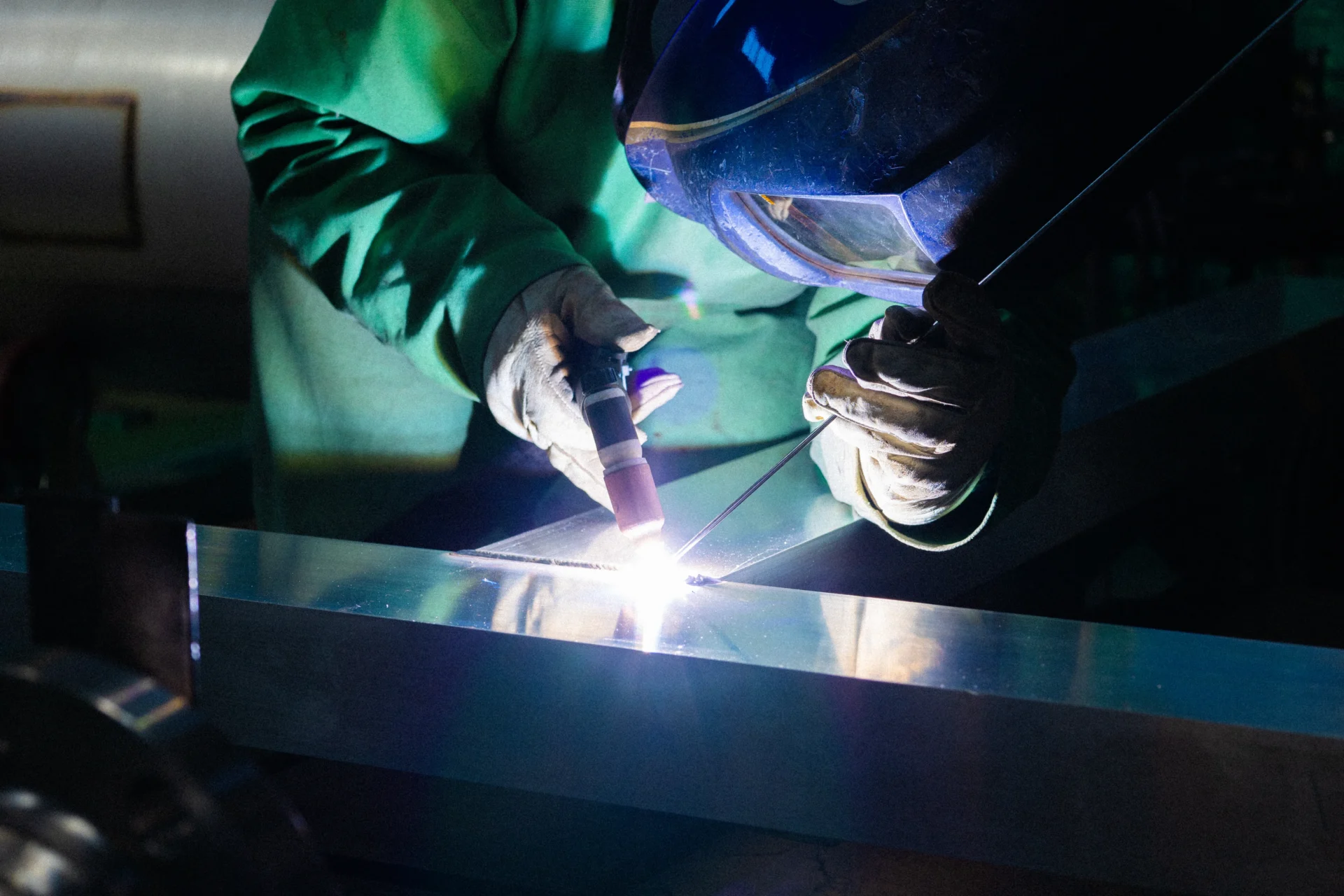
金属は加熱・加圧により、融点に達した際溶け始めます。
溶接はの基本的な仕組みは、接合したい二つ以上の材料(金属やプラスチック、セラミックス)を溶かして、接合部を融合させ冷やし固め一体化させます。溶接はその特性上、職人の技術力の差が大きく出やすく、溶接に関する技術を習得し、最適な溶接品質を確保するには長年の経験とノウハウが必要になります。
溶接方法は非常に多様で、使用する材料や目的に応じて多くの異なる加工方法があります。
溶接は、大きく分けて「融接」「圧接」「ろう接」の3つに分類されます。
融接は母材同士を溶かしたり、母材を接合するための溶接棒と母材を溶かして接合する加工方法です。
圧接は、圧力や電流、摩擦などで母材を溶かして接合する加工方法を指します。
また、ろう接は接合するための「ろう」(溶接材料)を接合部分の使用することで接合する加工方法です。
さらに上記から細分化された加工方法があり、求められる機能や製品ごとによって最適な溶接法を使い分ける必要があります。
溶接で用いられる材料には様々な種類があります。
主に金属が使用されていますが、特定の条件下ではプラスチックやセラミックスも溶接されています。それぞれ素材によって加工のしやすさや強度などが異なり、用途や製品ごとに用いる材料を選択する必要があります。
以下は溶接に主に使用されている材料です。
- 鋼(Steel)
最も一般的に溶接に用いられている材料で、カーボンスチールや合金鋼、ステンレス鋼があり、耐腐食性が求められる製品に使用されることが多い材料です。
- アルミニウム
軽量でありながら高い強度を持つため、航空宇宙産業、自動車産業、造船産業などでよく使用されています。ただ、アルミニウムの溶接は高度な技術力を要する場合が多く、非常に難しい溶接となります。
- チタン
高い耐腐食性と強度、軽量性から医療機器や化学処理施設などで使用されています。チタンの溶接では高い純度の保護ガスが必要になるなど技術的に難しい場合があります。
- ポリエチレン
パイプラインや化学タンクなど、多くの産業分野で使用されています。
- ポリプロピレン
軽量で耐化学性に優れており、医療器具や自動車部品などに用いられています。
以上の材料は、溶接法の種類や接合される部品の性質、製品の用途に応じて適応したものを選択する必要があります。専門的な知識と適切な溶接技術が求められるため、選択には慎重な判断が必要です。
溶接は非常に多様な製品と構造物に用いられており、日常生活から産業用途まで広範囲にわたって使用されています。例えば、自動車産業や建設業、航空宇宙産業、エネルギー産業など現代社会のインフラと製品製造において、溶接は中核的な立場を担っています。
溶接の主な種類
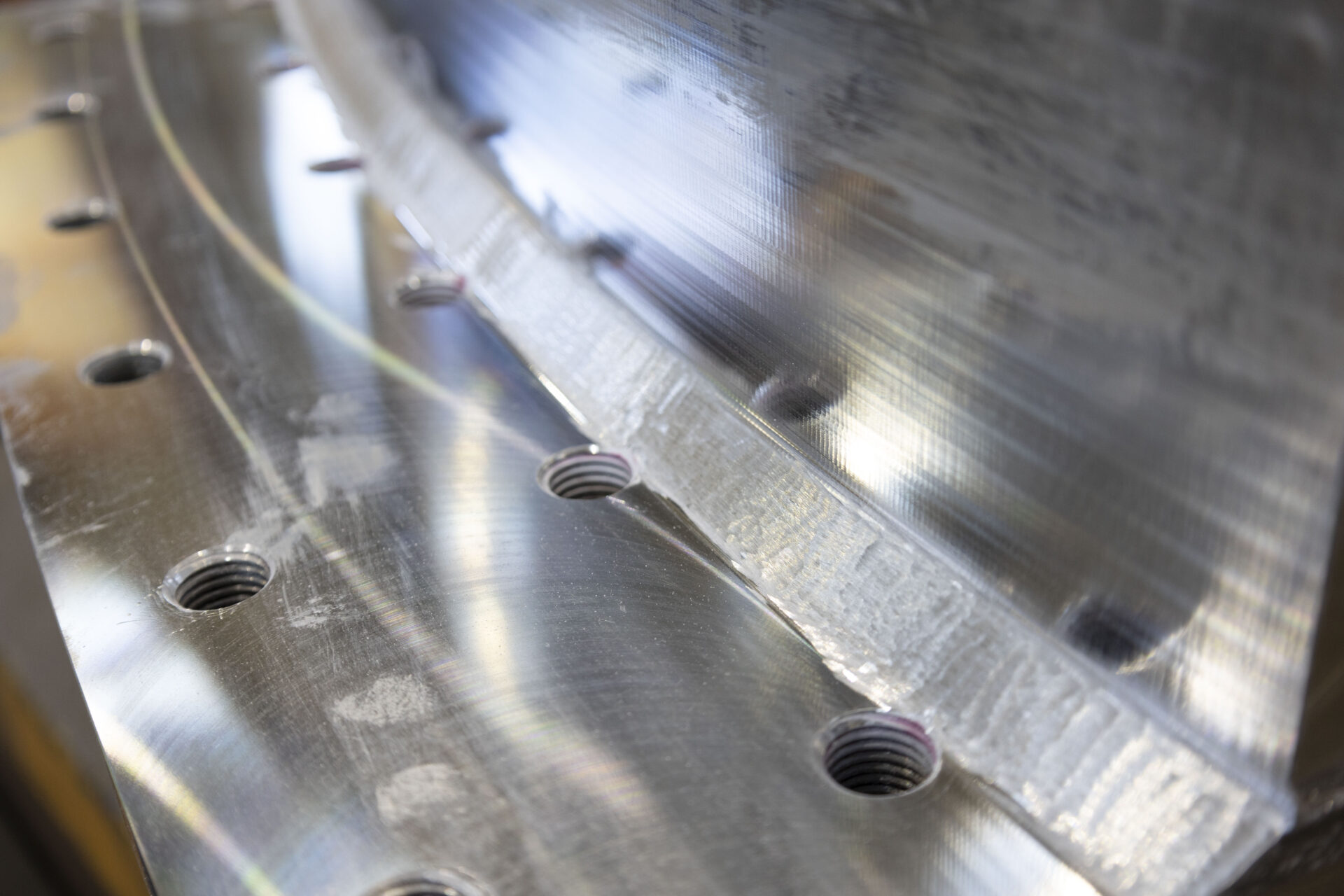
幅広い分野で用いられている加工法である溶接ですが、前述したように溶接方法も、用いる材料や求められる要件により多岐にわたります。
ここでは溶接方法の主な種類をご紹介します。
前述したとおり、溶接法には大きく「融接」「圧接」「ろう接」の3種類あります。それぞれ詳しく特性を見ていきましょう。
1.融接
融接は、接合される材料を溶かして結合する方法で、通常追加の充填剤を使用して融合した材料を補強します。融接では接合部を高温で融解させるため、元の材料と同等またはそれ以上の強度を持つ接合が可能になります。
自動車の製造や船舶建造、建築構造物など強度が要求される場面で多く使用されており、アーク溶接やガス溶接、レーザー溶接が融接の分類になります。
2.圧接
圧接は、加熱または加熱しない状態で材料を圧力で押し合わせることにより接合する方法です。正式名称は「加圧溶接」と言い、過熱を伴う場合もあれば、冷間で行う場合もあります。
材料を融解させずに接合するため、材料の劣化が少ないのが特長です。圧力は機械で設定されるため、技術にバラツキが起きることがなく、一定の品質に保つことができます。特に、摩擦圧接法や抵抗スポット溶接といった圧接法は、自動化や無人化が可能なことから、自動圧接機が導入されている事例も数多くあります。
3.ろう接
ろう接は、母材を溶かさずに、融点が母材より低い金属である溶加材「ろう材」を溶かして二つの材料を結合する方法です。ろう材が固まることで部品が結合します。母材同士が一体化した接合ではないため、ほかの溶接方法とは強度は劣ります。
母材を溶かさないため、材料の変形や損傷のリスクが少なく、様々な金属や非金属を結合できる汎用性があるのも大きな特長です。
ろう接は電子部品のはんだ付けや宝飾品の修理など精密な結合が必要な場面で使用されることが多く、加熱の方法により「アークろう付」「抵抗ろう付」「トーチろう付」など、ろう接の中でも分類があります。
溶接は大きく以上の「融接」「圧接」「ろう接」の3種類に分けられますが、その中でも加熱方法や装置の仕組みなどで細かく分類されています。用途に応じて最適な溶接方法を選択する必要があります。
以下に3種類の大分類ごとの代表的な溶接方法を紹介します。
融接 | ・ガス溶接 ・アーク溶接 ・ティグ(TIG)溶接 ・プラズマ溶接 ・ミグ溶接 ・被覆アーク溶接 ・電子ビーム溶接 |
圧接 | ・抵抗溶接 ・スポット溶接 ・シーム溶接 ・フラッシュ溶接 ・摩擦圧接 |
ろう接 | ・ろう付け ・はんだ付け |
以上のように、多種多様な溶接方法があり、それぞれ異なる利点や特有の特徴、用途があります。次の項目ではそれぞれの溶接方法について特徴を詳しく見ていきましょう。
種類別の特徴
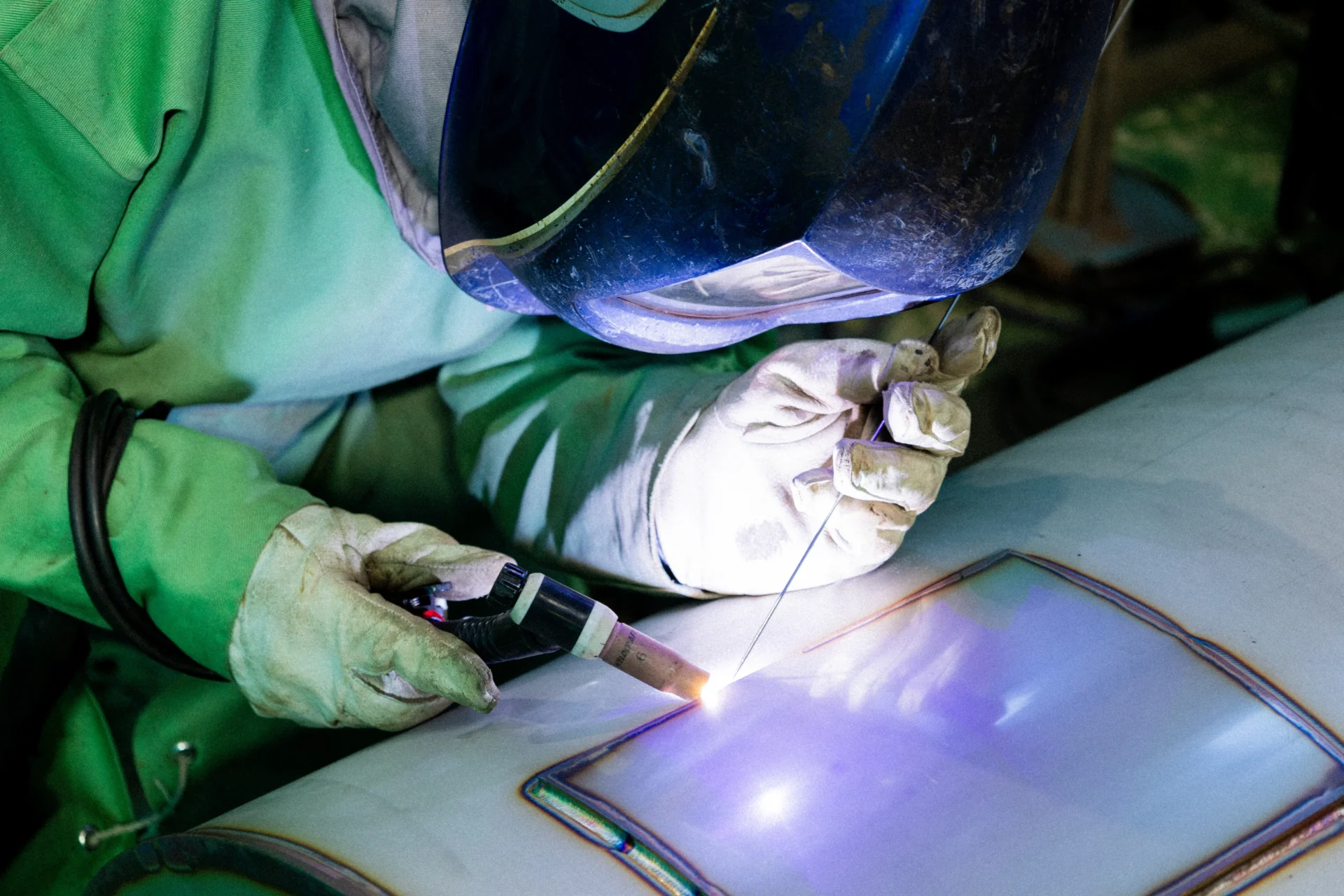
これらの溶接方法は提要する材料、必要になる強度、作業環境などにも応じて適切なものが選ばれています。どの溶接方法が最も最適なのかを見極めるには、それぞれの特徴をしっかりと把握する必要があります。
では、上記で紹介した溶接方法について、それぞれの特徴を詳しく見ていきましょう。
1.ガス溶接 - 融接
可燃性ガスを燃焼させて溶接したい部分を加熱する手法をガス溶接といいます。溶接速度が遅く、アーク光が発生しないので溶接部が見やすく、溶接不良を起こしにくいことが特長です。
そのため、高圧力がかかる油圧や空圧などの配管によく用いられています。ですが、機材の取り扱いには別途免許や資格(ガス溶接作業者)が必要になり、作業方法も比較的難しいことからあまり一般的とは言えません。
2.ティグ溶接(TIG溶接)- 融接
ティグ溶接はアーク溶接の一種で、融点の非常に高いタングステン電極棒を使用し、溶接したい部分を溶かします。シールドガスを用いることが一般的で、溶加材などを接合部に足すことも可能です。唯一溶接作業時に火花が散らない特徴があり、製品をきれいな状態に保つことができます。
ティグ溶接は高品質で精密な溶接が可能で、ロケットエンジンなどの精密機器によく用いられている手法です。ただ、作業の難易度は非常に高く熟練の技術力が必要となります。
3.被覆アーク溶接 - 融接
アーク溶接の基本である被覆アーク溶接は、溶接棒を使う溶接方法を指します。この手法は、風などに強いことから屋外での作業に適しており、装置が単純で持ち運びしやすいため現場での修理などによく用いられています。
ですが、使用する溶接棒は太く、大電流のアーク放電のため、薄板の溶接は不可能となっています。また、ほかの溶接法と比べて技術を要する方法であり、職人の技術力の差で品質が左右してしまう場合があります。
4.電子ビーム溶接 - 融接
電子ビームを溶接したい部分に当てて加熱する手法を電子ビーム溶接と言います。入熱量が少なく済むことから、溶け込みが深く精密な溶接をすることができます。また、異種同士の金属の接合も可能で、人工衛星や高エネルギー加速器の部品などに使用されています。薄板から厚板、さらに微細溶接まで可能で、ゆがみの少ない溶接が最大の特徴です。
ただ、真空中でしか溶接ができないのでコストは非常に高く、高価な技術となっている。近年ではこうした問題を解決する、完全な真空状態でなくても溶接ができる技術や機器が開発されており、利用範囲は徐々に広がっています。
5.スポット溶接 - 圧接
抵抗溶接の一種であるスポット溶接は、薄い板金を両側から抑えつつ電流を流し発生した熱を利用して溶接をする手法です。接合部に高圧を加えることで金属を一点で融合させます。抵抗溶接の中でもスポット溶接は最も一般的な形式で、自動車の製造ラインなどで広く使用されています。
溶接時間が短く生産性が非常に高いのが最大の特徴です。また、圧接は比較的技術力が必要ない手法なので、近年では産業用ロボットでの導入が広がっており、大物などの溶接はロボットが行う場合が多くなっています。
6.ろう付け - ろう接
ろう接の中でも、高融点のろう材を使用するろう付けは、ガス溶接用のトーチを使用する「トーチろう付け」や高周波誘導加熱を利用する「誘導加熱ろう付け」などがあります。ろう付けはステンレス鋼やチタン、セラミックスなどの接合によく用いられており、近年では「レーザーブレージング」といったろう付け技術が脚光を浴びています。
レーザーブレージングはワイヤ上のろう材を供給しながらレーザーでろう材を溶かして接合させる手法です。母材をほとんど溶かすことなく溶接することが可能ですので、熱変形を抑えた、デザイン性を担保した高い品質の接合ができるのが最大の特徴です。
溶接のメリット・デメリット
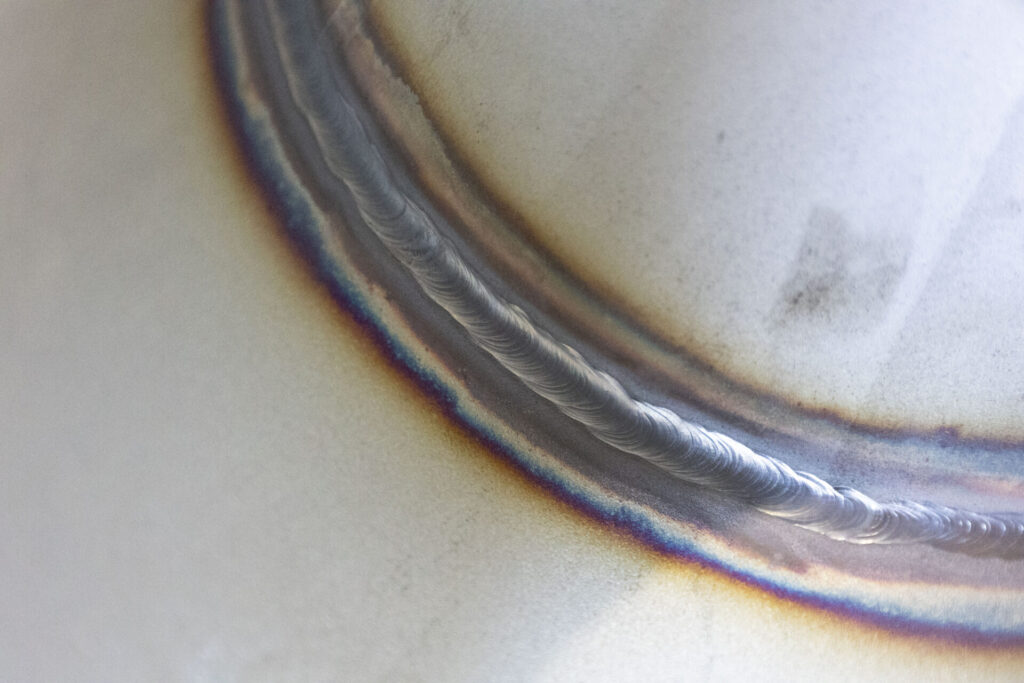
溶接は幅広い業界の製品に用いられており、多くの製造現場での不可欠な工程・技術ではありますが、用途や求められる技術によってはメリット・デメリットがあります。
それぞれどんなものが挙げられるか解説していきます。
1.メリット
- 自由度
溶接はその手法の広さから様々な材料や厚さに適用可能で、小規模な修理作業から大規模な建造物の建設に至るまで幅広い用途に使用されており、適切な方法を選択することができれば自由度を高く製品の製造が可能になります。また、様々な継ぎ手の形状に対応できるのも溶接の大きなメリットです。形状によっては求められる技術は高くなるものの、自由度の高さは他の加工方法と比べメリットとなります。
- 効率性
溶接は工程が他の加工方法よりも少ないため、効率良く作業することができます。また、圧接などの溶接法になると大量生産に向いており、自動化された工程を組み合わせることにより、生産性の向上と製造コストの低減に期待ができます。
- 気密性・耐圧性
ネジやボルトでの接合ではやはりどうしても隙間を完全に埋めることができませんが、溶接での接合では、金属同士を完全に接合してしまうので、気密性や水密性が高くなります。そのため、高圧での気圧や水圧に高い耐圧性を示します。
- 強度
正確に行われた溶接接合部分は、接合された母材と同等またはそれ以上の強度を持つことができます。(参照:日本溶接協会溶接情報センター「WE-COMマガジン」)適切な材料や溶接法を選択し、技術者による品質の高い溶接を実行することができると、溶接部は高い強度を実現します。
2.デメリット
- 技術要求度
溶接は高度な技術を要求するため、熟練した溶接工が必要です。不適切な溶接は、強度が不十分な接合や欠陥や不良を起こし、将来的に破損を引き起こす原因となります。
- 寸法精度
母材を溶かし融合させている溶接は寸法精度の維持が非常に難しいです。こうした問題があるため、レーザーでの位置決めをするなど寸法精度を上げるための対策が必要になります。
- 作業環境の制約
特定の溶接方法では(特にアーク溶接など)、風が強い環境や湿度が高い環境での使用には不向きです。一般的に屋外での作業のみとなり、作業環境が制限されています。溶接の中には屋外に向いた方法もありますが、使用用途や求める品質によっては不向きな場合があり、適切な溶接方法の選択が必要です。
以上のようなメリット・デメリットを正確に理解し、適切な溶接方法と対策を選択することにより、その効果を最大限に活かすことができます。
溶接加工における不良とその対策方法
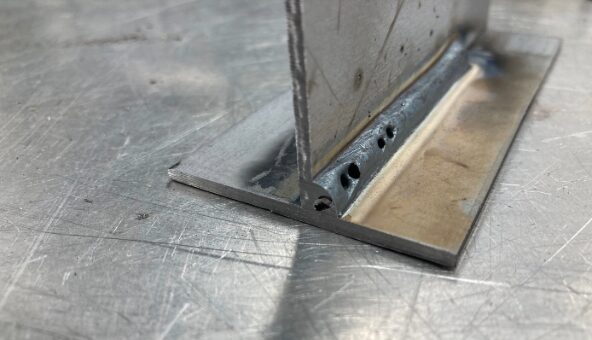
溶接加工においては、様々な不良が発生することがあります。これらの不良は構造物の安全性や耐久性に大きな影響を与えるため、適切な対策を講じることが重要です。以下に一般的な溶接の不良とその対策方法を説明します。
1.ピット・ブローホール
ピットは、溶接された金属の内部に発生したガス孔が表面に放出されたときに穴となって固まった表面欠陥を指します。また、内部のガス孔をブローホールと呼ばれる内部欠陥を指し、ピットとともに発生原因としてはシールドガスの不良や脱酸材の不足、母材面の油分やサビ・水分、表面付着材などが挙げられます。
溶接前には材料を適切に清掃し、油分や水分を除去することで大幅に不良は低減します。また、適切な熱入力やガス量を設定することが重要です。
2.アンダーカット・オーバーラップ
アンダーカットは母材または既溶接の上に溶接を行った際止端の溝です。溶接電流や溶接速度が過剰に高い場合に発生することが多く、強度が大幅に低下します。また、オーバーラップは母材表面にあふれた融解金属が、母材を融解しないまま冷えて固まることを指し、溶接速度が低い場合溶着金属量が過剰になり発生します。
溶接電流と速度を適切に調整し、一定の量と角度で施工することで不良の発生を抑えることができます。
3.クラック(割れ)
溶接直後の高温状態の際、溶接部やその周りに発生するひび割れを指します。金属が凝固する際に割れる場合や多層溶接時に前の溶接層が次の溶接により溶けて割れが発生する場合があります。材料の疲労や構造的弱点につながるため、十分な対策が必要になります。
溶接前に母材を予熱することで材料の冷却速度を遅くし、冷却時間を長くします。また、溶接金属の強度が強くなり過ぎないように調節することも重要で、発生応力を最小化することが必要になります。
当社の溶接加工事例
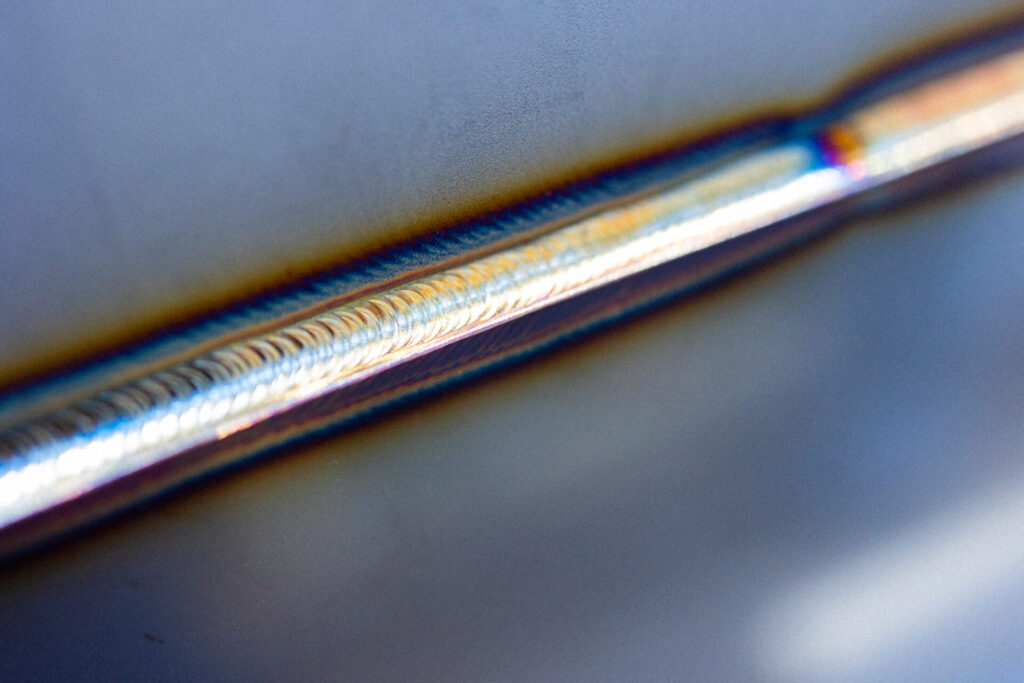
当社で行った溶接のビード
当社では多種多様なプロジェクトで培った豊富なノウハウと、一流の職人による確かな技術力を保持しています。高品質かつ高精度な技術が求められる溶接では、技術者による技術力の差が製品の品質を左右します。
計装配管から大径配管まで全管種においてプラント配管に特化した卓越した技術力と経験により、お客様の多様なニーズにお応えしてきました。お気軽にご相談ください。
以下、当社にて実際に製作した溶接の加工事例をご紹介します。
- 発電プラント内 大径管(SUS200A SCH120)溶接
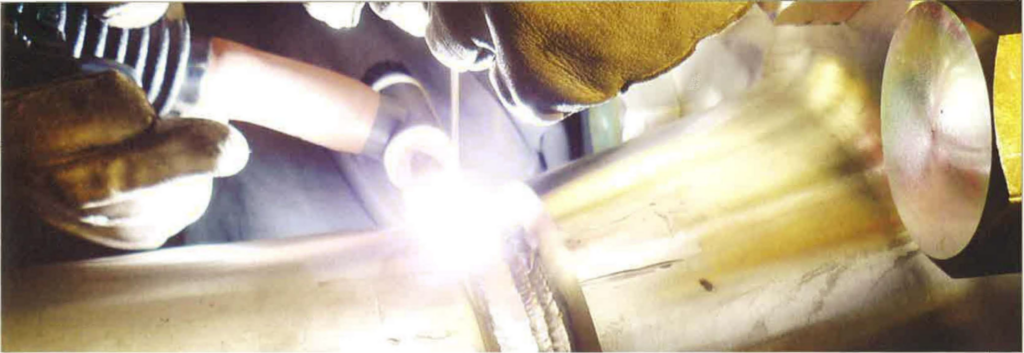
発電プラント内で利用する材質:SUS200A、厚さ:SCH120の大径管の溶接作業です。
高い技術を求められるステンレスかつ厚みを持つ材質なため、歪みを抑えるための予熱や後熱の考慮や
溶接材の選定など、弊社の強みである豊富なノウハウを活かした製品です。
材質 | SUS200A |
厚さ | SCH120 |
開発期間・納期目安 | - |
交差レベル | - |
製品用途 | 発電プラント |
- 発電プラント内 SUS大径管
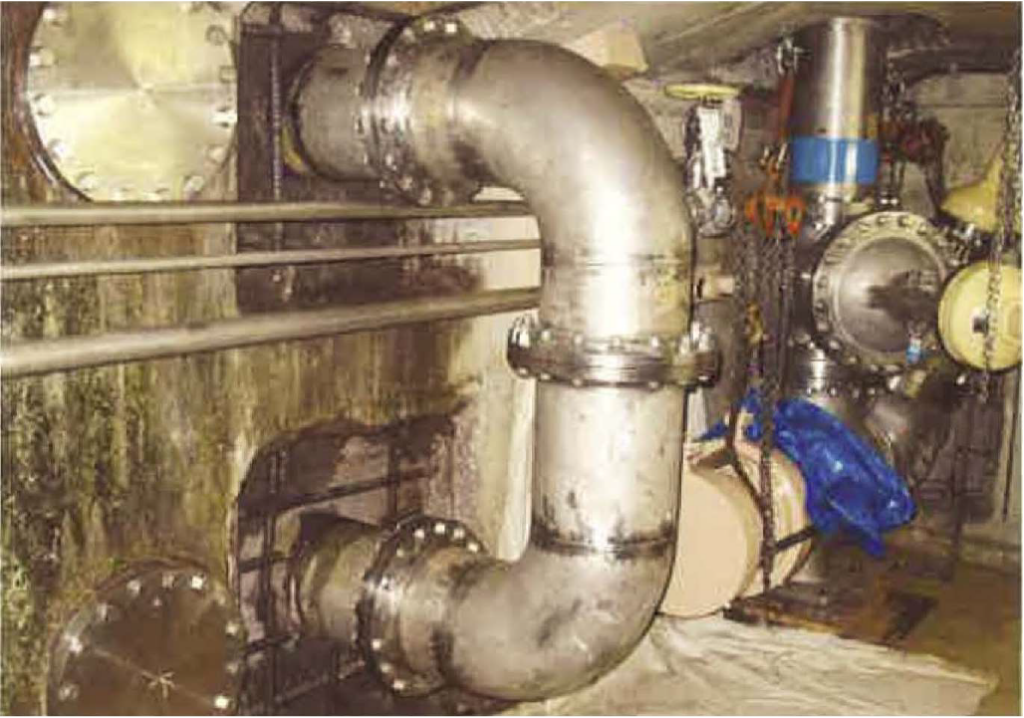
本製品は発電プラントにおけるSUSの大径管です。
ご要望に合わせた部材の製造から、現地の据え付け工事まで一貫にて対応しました。
大物品の取り付け工事となり、信頼性を担保する高い溶接技術が求められますが、弊社の強みであるプラント配管の多数実績と高いノウハウを活かした製品です。
材質 | SUS材 |
サイズ | |
開発期間・納期目安 | - |
交差レベル | - |
製品用途 | 発電プラント |
溶接とは?~まとめ~
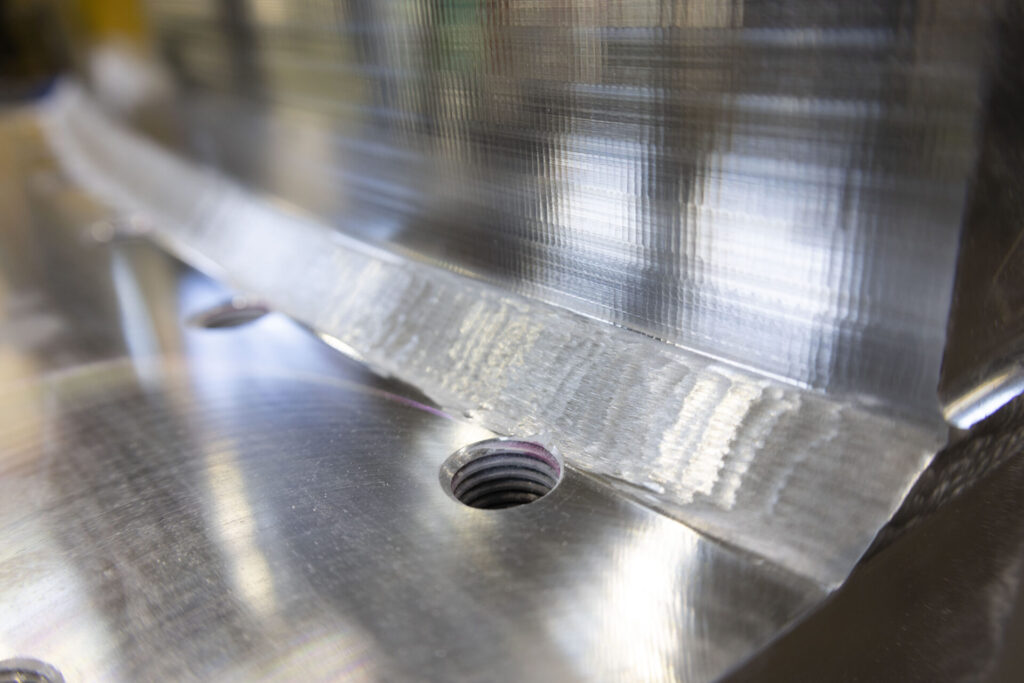
溶接技術は現代の製造業において不可欠な技術であり、その適用範囲は自動車から航空宇宙、建築に至るまで多岐にわたります。溶接には様々な方法があり、それぞれが使用用途や求められる要求により最適化されています。適切な溶接方法の選択と、正確な技術の実施は、製品の安全性と耐久性を大きく左右します。
また、溶接不良を防ぐための対策を理解し適用することは、高品質な製品を保証する上で極めて重要です。当社ではこれまでに培ったノウハウと高品質な溶接技術を基に、現地での据付作業や付帯する鋼構造物製作などプラント配管に関わる幅広いニーズにお応えし、お客様から高い信頼と評価を得ております。
溶接加工に関するご依頼をご検討中の方は、お気軽に当社までご相談・お問い合わせください。
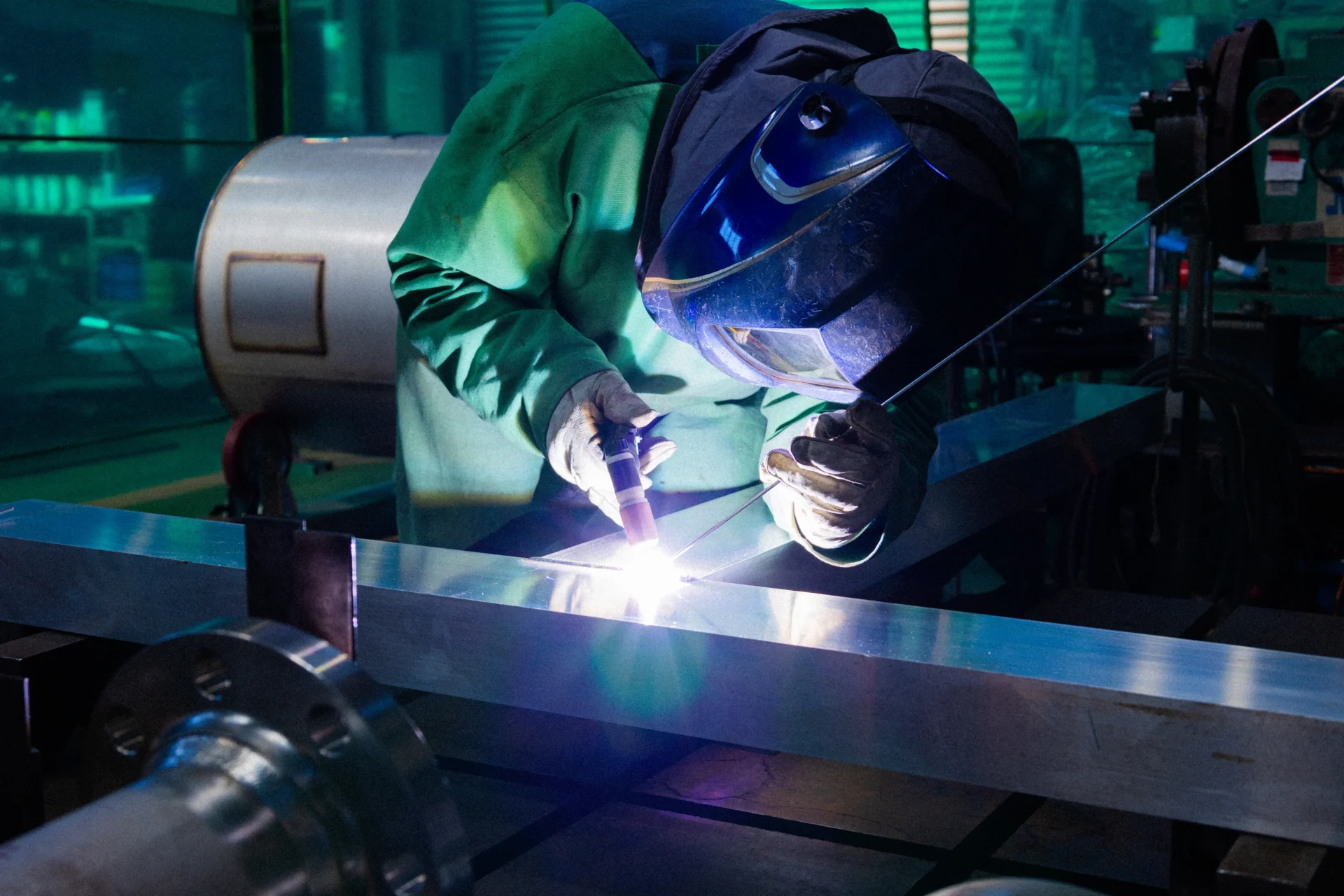
お問い合わせ
ご相談・お見積り依頼などお気軽にお問い合わせください